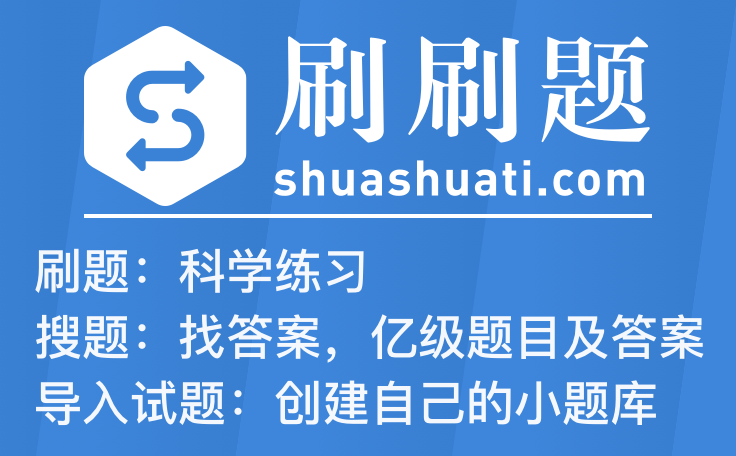
Cherry Blossom Co (Cherry) manufactures custom made furniture and its year end is 30 April. The company purchases its raw materials from a wide range of suppliers. Below is a description of Cherry’s purchasing system. When production supervisors require raw materials, they complete a requisition form. and this is submitted to the purchase ordering department. Requisition forms do not require authorisation and no reference is made to the current inventory levels of the materials being requested. Staff in the purchase ordering department use the requisitions to raise sequentially numbered purchase orders based on the approved suppliers list, which was last updated 24 months ago. The purchasing director authorises the orders prior to these being sent to the suppliers. When the goods are received, the warehouse department verifies the quantity to the suppliers despatch note and checks that the quality of the goods received are satisfactory. They complete a sequentially numbered goods received note (GRN) and send a copy of the GRN to the finance department. Purchase invoices are sent directly to the purchase ledger clerk, who stores them in a manual file until the end of each week. He then inputs them into the purchase ledger using batch controls and gives each invoice a unique number based on the supplier code. The invoices are reviewed and authorised for payment by the finance director, but the actual payment is only made 60 days after the invoice is input into the system. Required: In respect of the purchasing system of Cherry Blossom Co: (i) Identify and explain FIVE deficiencies; and (ii) Recommend a control to address each of these deficiencies. Note: The total marks will be split equally between each part.