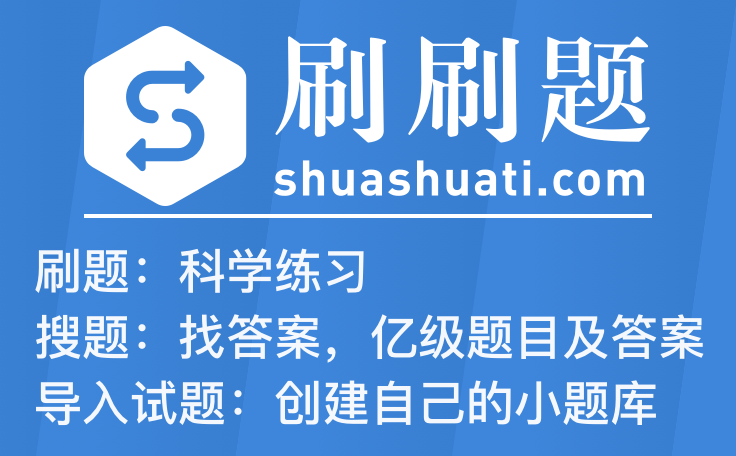
Because the aircraft industry needs ever-increasing quantities of aluminium plate, new equipment has been designed to automate the making of it. It includes a huge heat-treatment furnace, a crane that lifts hot metal plates without damaging them, and a computer system that can manage the complete flow of work. Five years ago, Europe's aircraft industry needed only 8,000 tonnes of aluminium plate a year for its products. Last year the figure reached 21,800 tonnes. By 2004 it should total 30,000 tonnes. Each airliner contains 180 tonnes of it. That is why the plant is being rebuilt to increase both the quality and the amount of its product. Aluminium is alloyed with other metals and cast into ingots, and the surface of the ingots is smoothed off. After pre-heating, it is rolled in a mill that can take 3.75-m-wide slabs. The new equipment can make the process more efficient and can produce a better product. For example, computers control the temperature of the hot plates, the rate at which they pass through the mill, the speed of cooling it with water, and so on. The new plant can handle twice the throughput of the one that it is replacing, thanks to the completely automated and computerized process.